Compressors or compactors are one of the types of utility tools in most large industries that have a variety of applications. This device compresses all kinds of fluids, especially air. In fact, compressors suck air in with the help of electric energy and after compressing it, they take it out with high pressure. There are different types of air compressors, each of which has different capabilities. One of these types is the centrifugal compressor, which is also known as the centrifugal compressor and is an industrial wind pump.
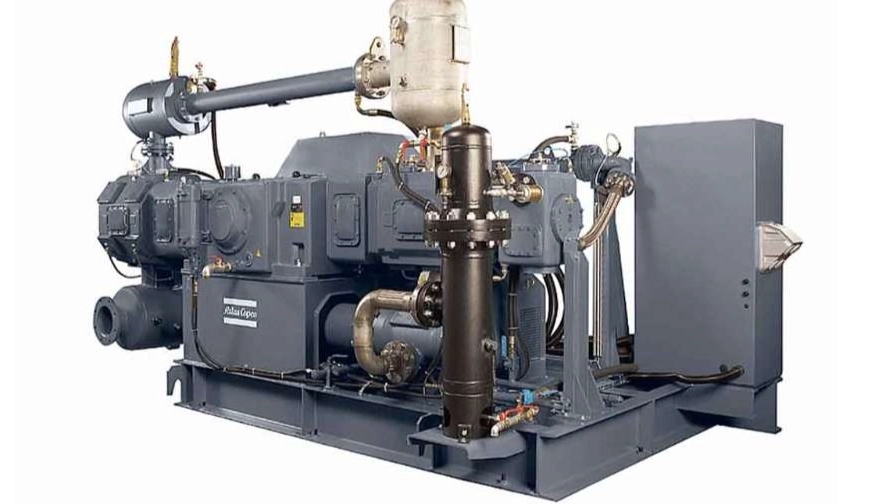
Centrifugal compressor is a type of refrigeration compressor that is also known as turbo. This device increases air pressure by using centrifugal force; That is, the rotation of the propeller causes the air to enter the compressor axially and be compressed and thrown out by the acceleration of the propeller.
Types of centrifugal compressors
Centrifugal compressors are divided into single-stage and two-stage or multi-stage types based on the mode. Single stage compressor
In this compressor, only one propeller is used to compress the air and they are used at low pressures. In single-stage compressors, the impeller is located at the top of the rotor. The features of this compressor include simple design and easy operation.
Two-stage or multi-stage compressor
In this type of compressor, according to the working stages, the cylinder is located with different drops and between each compression stage, an intercooler or cooling It is located to reduce the temperature. Among the advantages of this type of compressor compared to single-stage compressors, we can point out humidity reduction, greater efficiency and reliability. Centrifugal compressors are also divided into two types of oil and oil-free centrifuges based on the lubrication method.
Centrifugal compressor components
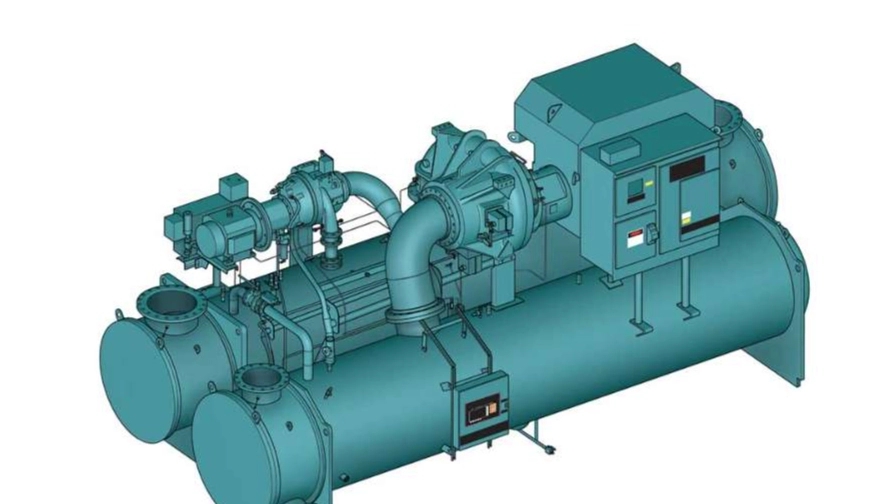
A centrifugal compressor consists of 4 main parts, which include the following: 🔷 Inlet port: The inlet is a tube that includes a blade or airfoil, a valve, and some temperature and pressure measuring devices. 🔷 Propeller: The propeller is one of the main parts of the compressor, which increases the energy of the gas with its movement, and the larger the radius, the more energy it has. 🔷 Diffuse: Diffuse is the place of gas compression and has different types such as finned, finless and combined. 🔷 Collector: The collector is the final part of the centrifuge, whose purpose is to collect the exhaust gas from the diffuser.
Application of centrifugal compressor
Centrifugal compressors have many applications in various industries, the most important of which are the following: Use in power plant industries One of the most important applications of centrifuge is the use in the electricity industry. Also, these compressors are used in industries such as gas, hydroelectric, nuclear, solar and geothermal. The source of production of power plants is natural gas, and to carry out primary combustion, air must be compressed. Therefore, the role of centrifugal compressor in these industries is very colorful. Use in aviation industry The engine of small airplanes is rotary and one of the most important parts in the airplane is the propulsion force to move it. For this reason, a jet engine is used. This engine draws air in and uses fuel injection to mix it with air, which causes its combustion. It works like a centrifugal compressor. The end of this product (nozzle) provides the necessary propulsion power for the aircraft and the small turbine is moved by the mixture of fuel and air. This force is able to move the shaft in the compressor and the centrifugal compressor is placed in front of it. Use in the automotive industry If the air entering the car engine is compressed, it can increase the required force. For compression, turbocharger and supercharger are used, whose function is similar to the centrifugal compressor, and like that, they get their power from the exhaust gases.