What is a plastic injection machine?
Today, the use of plastic injection machines has become very common in the production industry. Plastic has a good price and it is easy to shape, for this reason it has found almost the largest share in human life and is used in industries such as automobile manufacturing, electronics, air and space, medicine, construction, toys, etc. Placed. Due to the abundant profits of this industry, it has gained many fans.
History of plastic injection machine
About a hundred years have passed since the life of plastic. Until about seventy years ago, no one was aware of the existence of this industry in its present form and scope. Cellulose is one of the first pseudo-plastic materials obtained from nature and used by humans. A substance called caoutcho was used in industry from the gum of forest trees. Around 1870, the exploitation of cellulose acetate materials began. From 1906 to 1909, a person named B. Kland managed to prepare the first plastic material through industrial chemistry, and this plastic became known by its own name, Bakelite. For the first time, John Wesley Haight used celluloid injection into a mold to produce billiard balls in 1868. By optimizing the celluloid, Wesley made it ready for processing and making the final shape. The first injection machine was built by John and his brother in 1872, which is simpler than today's machines and has fewer components. The device made by John has a piston that passes the material through the heated cylinder and is injected into the mold. With the slow progress of the industry over the years, other products such as shirt collar shapers, buttons and pocket shoulders were produced. In the 1940s, due to the large demand for cheap and mass-produced products during World War II, the concept of injection molding saw a significant growth.
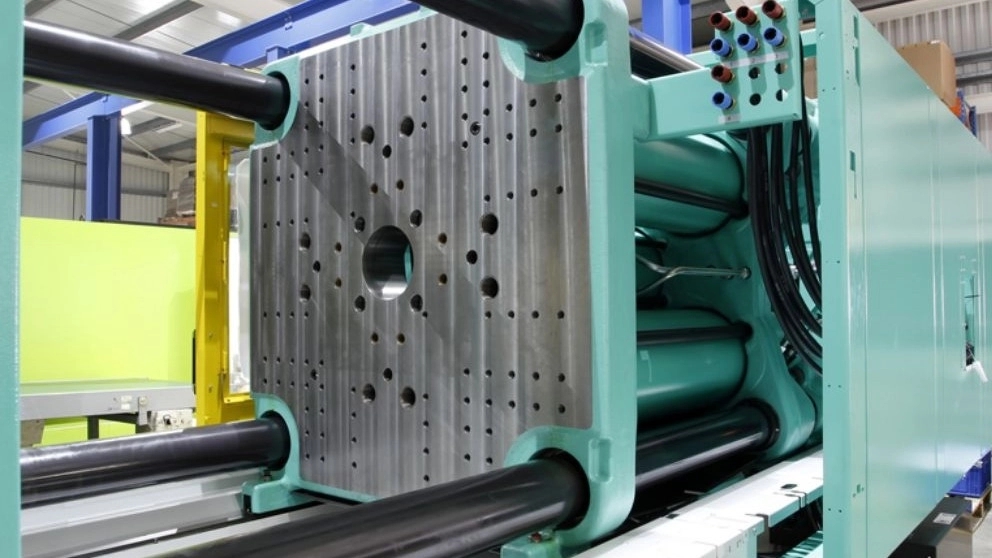
In 1946, James Hendry invented the first screw injection machine and revolutionized the plastics industry. In his device, the piston was replaced by a designed drill. This drill guided the materials inside the cylinder before injection, mixed and then into the mold. In this way, before the injection operation, the possibility of combining and mixing colored or recycled plastic with raw materials was completely possible. Today, spiral injection machines make up 95% of the production share of related companies. The industry of injection moldings has evolved from the production of shoulder and button to the production of medical, aerospace, toy, packaging, automotive and construction products, gradually and over many years. After a part is designed by an engineer or an industrial designer, a mold is made according to the part by a mold maker. Injection molds are generally made of steel or aluminum and are carefully machined to reflect the features of the designed part. Injection molding is used to produce a wide range of products from the smallest objects to the complete body of automobiles.
Capabilities and limitations of plastic injection
Plastic injection is the most cost-effective technology for producing identical plastic parts in high volumes. A wide variety of raw materials are available for plastic injection, the physical properties of these materials can be customized depending on the requirements of your design. Plastic injection provides manufacturers with high repeatability along with high production speed (a manufacturing cycle usually takes less than 60 seconds).
The cause of weld lines in plastic injection parts
The piece has many holes. The part has many details that interrupt the flow of plastic injection. Molten plastic is injected into the mold through several gates. In order to prevent these problems, it is better to limit the number of holes or use more viscous plastic compounds. When injecting plastic, air may get stuck in dead end parts of the part (parts that are closed on one side) and the air pressure prevents the flow of plastic into the part. This issue causes some areas of the part not to be completely filled with compressed plastic. The temperature of this trapped air in the part can rise and burn parts of the part. This problem can be prevented by adding ventilation holes in critical points.