Production methods of ferroalloys
There are many methods for producing ferroalloys, most of which are produced by pyrometallurgy. The production methods of ferroalloys are mainly divided into the following based on the melting equipment, operating methods and heat sources used:
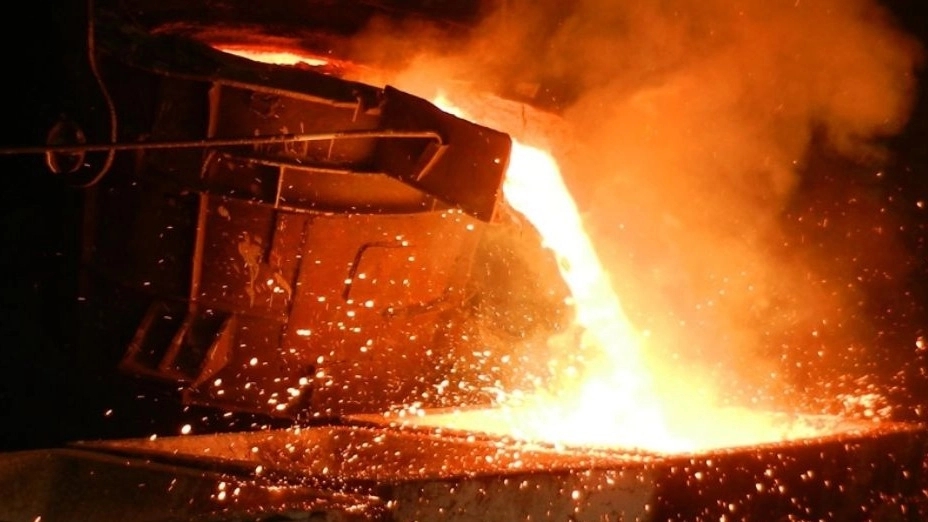
Classification based on production equipment
According to the production equipment, it can be divided into blast furnace method, electric furnace method, out-of-furnace method, converter method and vacuum resistance furnace method. electric furnace method Electric furnace is the main method of producing ferroalloys and its output is about 80% of all ferroalloys.
The blast furnace method The main equipment used in the blast furnace method is the blast furnace. The blast furnace method is the first method of ferroalloy production. The blast furnace process has advantages such as high labor productivity and low cost. However, due to the temperature limitation of the blast furnace and the complete saturation of the metal with carbon during the blast furnace melting process, this method is usually only used to produce ferroalloys with reducing elements and low-grade ferroalloys.
out method From the furnace (metal thermal method)
The out-of-furnace method uses silicon, aluminum, or an aluminum-magnesium alloy as a reducing agent, and melting occurs by relying on the chemical heat produced by the reduction reaction. . The main equipment used is a cylindrical furnace. The raw materials used include concentrate, reducing agent, flux, heating agent, steel shavings, iron ore, etc.
< font color="#000000">Oxygen converter method
< p style="text-align: justify;">The main equipment used in this method is the converter . According to the method of oxygen supply, there are composite blowing methods from top to bottom, from the side, and from bottom to top. The primary materials used are high-carbon liquid ferroalloy, pure oxygen, cooling materials, slag generator, etc. High-carbon liquid ferroalloy is added to the converter and high-pressure oxygen is blown into the furnace through an oxygen gun. . The production is carried out intermittently, depending on the heat from the oxidation reaction.< span style="font-size: 14px; white-space: normal;">
Vacuum resistance furnace method
< p style="text-align: justify;">Vacuum resistance furnace for producing ferrochrome products It is used with microcarbon, ferrochromium nitride and ferromanganese nitride with very low carbon content. The main equipment in this method is the vacuum resistance furnaceClassification based on heat source
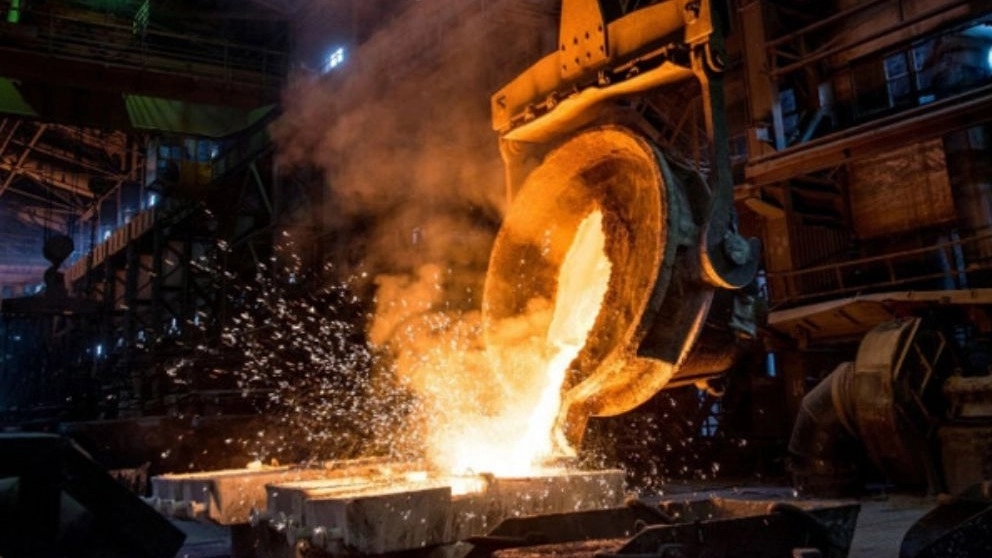
Classification based on method and process of operation
According to the characteristics of the production and exploitation process, it can be divided into flux method, solvent-free method, slag-free method and continuous and intermittent melting method. Flux method Smelting iron alloys by flux method uses carbon materials, silicon or other metals as a reducing agent. Slag-forming materials must be added during production to adjust the composition and properties of the slag. If alkaline slag is used, ferromanganese with high carbon content can be produced. Method without flux In general, carbon materials are used as reducing agents in the production of flux-free ferroalloys. The composition and properties of slag are not adjusted by adding slag-forming materials in production. If high-quality manganese ore is used, acid slag is used to produce ferromanganese with high carbon and low phosphorus, and a manganese-rich slag is obtained. method without sludge Sludgeless smelting of ferrous alloys is a continuous smelting process in a reduction furnace using carbon reducing agent, silicon or regenerated alloys as raw materials. The products include ferrosilicon, industrial silicon, chrome-silicon alloys, etc. method with sludge Slag smelting of ferroalloys is the production of ferroalloys in electric recovery or purification by choosing the type of slag system and appropriate basicity. The ratio of slag to iron is affected by different types and conditions of the respective raw materials. Products include high carbon ferromanganese, manganese silicon alloy, high carbon ferrochrome, etc. Continuous melting method The method of continuous melting is that the furnace is continuously charged according to the drop of the charge level in the furnace opening, while the alloy and slag accumulated in the furnace basin are discharged regularly. With submerged arc regenerative melting, the operating power is almost equal and stable. periodic melting method Batch melting is a process in which the charge is concentrated in a furnace or as a batch, and is generally divided into two stages: melting and refining, in which the electrode is covered by the furnace charge.