Wire tension is a phenomenon in which a wire or metal wire is subjected to tension and changes its shape. This change in shape is due to changes in the level of crystal lattice and also the movement of metal particles in the environment. In pulling the wire, the tensile force causes the energy transferred in the wire, and this energy can be used to perform various tasks.
Wire tensioning device
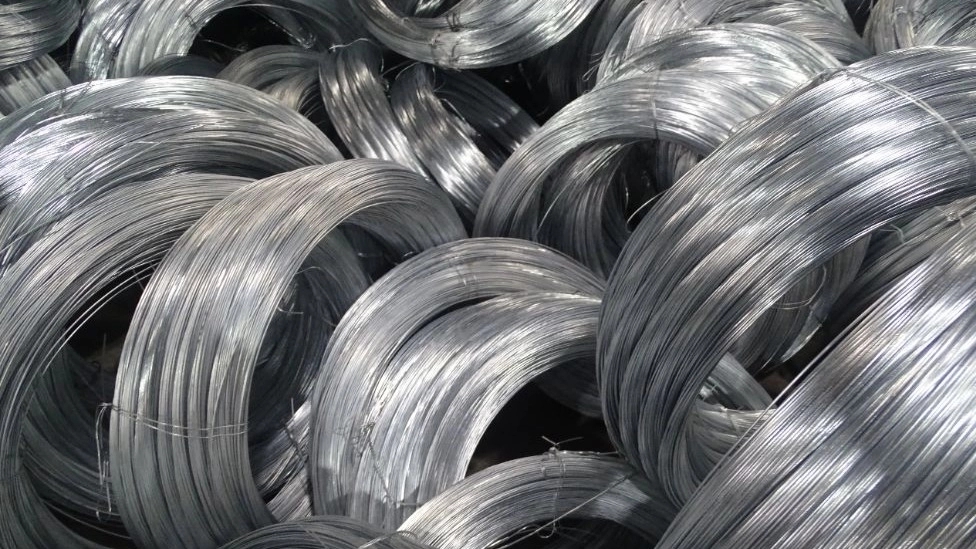
is a device that has one or more cable tension units to reduce the cross section. With wire drawing machines, the drawing is done mostly at room temperature, so the wire is cold worked. The main parts of the wire tensioning machine include the body, dynamo, gearbox, drum, reel and doze. The metal body is one meter wide and about six meters long. The device has an internal lubrication system and the telescopic wires are lubricated with different types of lubricants at each stage. Lubrication in this machine is necessary to improve the quality of the final surface of the product and to prevent premature damage of the mold. Considering that after each stage of drawing the cold wire, the effect of cold working may cause a partial loss of its properties, so it is recommended to anneal the wire to reduce the effect of cold working. In this case, an annealing furnace with a device is required. In addition, annealing can increase the flexibility and electrical conductivity of the product. Alternatively, the furnace can be used to increase the temperature of the large diameter wire, as it is sometimes necessary to heat the wire to reduce the tensile strength.
Types of wire tensioning devices
What makes the traction machine different is the number of drums installed in the machine. Some machines have one drum and some have up to twenty drums. The power of the unit depends on the size of the drum, the power (horsepower) of the gearbox and the alternator. The wire tension device is a laboratory device that is used to check the behavior of materials under tension. This device includes several key parts that we will mention below:
1. Sample substrate: In this device, the tested sample is placed on a substrate. This substrate is able to apply the desired stress to the sample and record its shape change. 2. Sensors: In the wire tensioning machine, various sensors are installed to detect shape changes. and measure the tension. These sensors transmit the necessary information to the laboratory device.
3. Laboratory machine: The wire tension device uses a laboratory machine to apply tensile forces on the sample. This machine is able to apply the desired tension on the sample and record its deformation. 4. Control software: Control software is installed in the wire tensioning machine. It provides the possibility to control and record information. This software is able to analyze the test results and produce the required reports. It is used appropriately. These sensors are usually placed at strategic points on the wire to measure changes in length. The sensor system usually consists of semiconductor transducers and sensitive coils that convert shape changes into electrical signals. These signals are then transferred to the control device and can be used to analyze and check the test results.
How the wire tension machine works
The wire tension device works as follows using a laboratory machine and various sensors:
1. Placing the sample: The sample to be tested is placed on the substrate. The sample must be placed correctly and carefully on the substrate so that the test results are accurate. 2. Applying tension: The laboratory machine applies the desired tension to the sample. The tension can change directly or proportionally with time. 3. Data recording: The sensors receive the information related to deformation and tension and send it to the control device. This information is recorded in the control software and can be analyzed and checked. 4. Analysis of the results: Using the control software, the test results are analyzed. This analysis includes the examination of shape changes, stress and mechanical properties of materials.