Aluminum is a light but strong metal that has good thermal and electrical conductivity. Aluminum alloys are available in different categories, one of which is casting type.
All kinds of aluminum casting alloys
200 series aluminum casting alloys: In this alloy, the main element is copper, which has recently been replaced by elements such as magnesium, aluminum, and silica, which has contributed to lower weight and better corrosion properties. This series has different types, its 242 and 222 series are used for casting pistons.
300 series aluminum casting alloys: In this category, which is one of the most widely used aluminum casting alloys, alloys such as magnesium, aluminum, silicon and sometimes copper are used. Among the alloys of this series, 354, 333, 308 and 319 can be mentioned, which are used to make parts of car engines, cylinder heads, permanent molds, rocket and airplane parts.
400 series aluminum casting alloys: this type is the simplest and most widely used alloys of this series, the most used element in which is silicon, which is more than 5%. This series is used for casting parts that have complicated shapes. In this category, there are alloys such as 433 and 413, which are mostly used in sand.
500 Series Aluminum Casting Alloys: This series of alloys is produced from the combination of magnesium and aluminum and its use is limited. Today, in many applications, instead of using this group, they use the 300 series.
Aluminum casting alloys 700 and 800 series: Another type of casting alloys are the 700 and 800 series, which are formed by adding zinc and tin. These alloys have a specific and limited use.
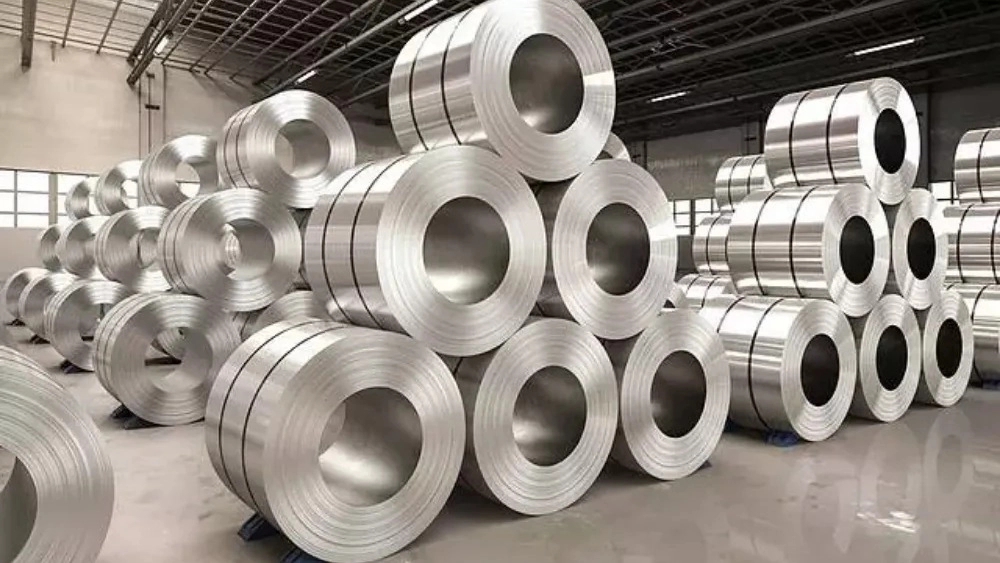
Their uses and properties
This alloy has good resistance against chemical and atmospheric corrosion. Compared to steel, it has a higher thermal conductivity and a lower melting temperature. Another property of aluminum casting alloy is its high electrical conductivity. Welding, nailing and riveting are easy in this material. It can be recycled and its casting can be done easily. It also has high strength compared to its weight. Due to these properties, this material is used in various applications. This product is used in the manufacture of engine parts, important components of airplanes and spacecraft. This alloy is used in making large and complex parts. Another use of this alloy can be mentioned in the production of truck parts, crankcase, air manifold.
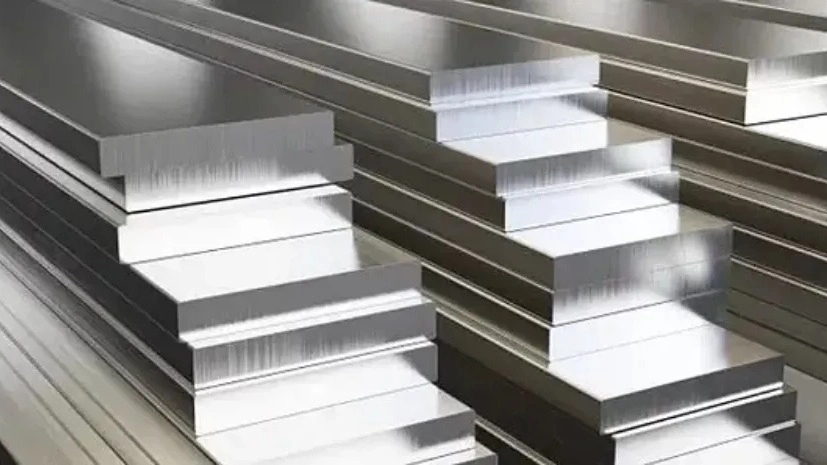
Application of aluminum casting alloy
First category: This category is not suitable for operations where the pressure is high, and it is suitable for the production of collector rings, transmission cables, rotors of electric motors, conductive rods, etc. Second category: This series of alloys has high strength, but it is not suitable for casting under pressure. It is used in the production of military and aerospace hardware, making diecast parts, making trailer and truck parts Third category: This series has high casting ability and has high strength. This category is used in the production of car cylinder heads, crankcases, iron soleplates, car pistons, counters, degrators, airplane parts, and air manifolds. Also, this material is used in the manufacture of electrical parts, commercial parts, aerospace and military industries. The fourth category: another application of cast aluminum alloy is in the manufacture of marine industry parts, chemical industry and feed transportation. The corrosion resistance of this category is good. Fifth category: These are of high quality and their resistance to corrosion is good. These cast aluminum alloys can be used in the production of pipe fittings, marine industry, marine industry parts, decorative parts, etc.
The importance of alloy selection and their characteristics
Choosing the right alloy in the casting process is a determining factor in the quality and performance of the final piece. Each alloy has a unique combination of elements that gives it different physical, mechanical and chemical properties. These properties include strength, hardness, corrosion resistance, melting point, thermal expansion and many others. Choosing the wrong alloy can lead to numerous problems including cracking, deformation, reduced component life and increased production costs. Therefore, a deep understanding of the types of casting alloys and their properties is essential for engineers and manufacturers dealing with this process.
Casting alloys
Copper alloys
Copper alloys are used in various industries due to their excellent mechanical and electrical properties. These alloys have electrical and thermal conductivity, corrosion resistance. Brass and bronze can be mentioned among copper alloys. Brass is an alloy of copper and zinc that has good mechanical properties and is used in the production of parts such as valves and fittings. Bronze is an alloy of copper and tin that has corrosion resistance and high strength and is used in the production of pieces such as sculptures and musical instruments.
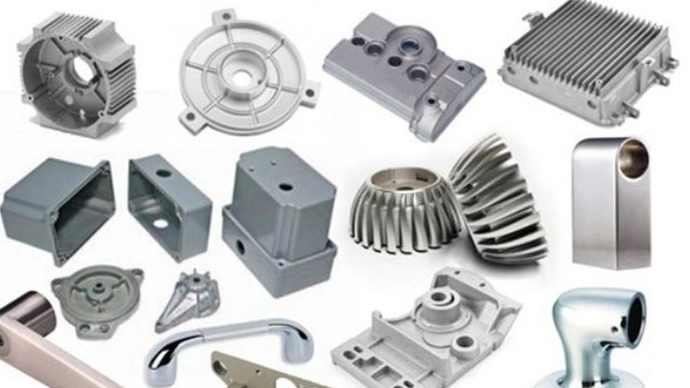
Zinc alloys
Tin alloys
Tin alloys are used in the production of components that require high accuracy due to its anti -corrosion properties and low melting points. These alloys are also used in the food and packaging industry. One of the most famous tin alloys is solder, which is a combination of tin and lead and is used in electronic components. This alloy has a low melting point and good mechanical properties that allow small, sensitive parts to connect.
Aluminum alloys
Aluminum alloys are widely used in the aerospace, automotive and construction industries due to their light weight and high corrosion resistance. These alloys have good mechanical properties and have high casting capability. One of the most famous aluminum alloys is Doravine, which is a combination of aluminum, copper, magnesium and manganese. Durialine is high strength and light weight and is used in the production of aircraft and automobiles.
Lead alloys
Lead alloys are used in the production of batteries and electronic components due to its anti -corrosion properties and good casting capability. These alloys have high density and low melting point. One of the most famous lead alloys is lead solder, which is a combination of lead and tin and is used in electronic components. Leader solder has good mechanical properties and allows small and sensitive parts to connect.
The best casting alloys
Choosing the best casting alloys depends on the specific needs of each project. Some popular alloys include aluminum, copper and zinc alloys, which are used in many industries due to excellent mechanical and physical properties. Aluminum alloys are widely used in the aerospace and automotive industries due to their light weight and high corrosion resistance. Copper alloys are used in the electronics and electricity industries due to high electrical and thermal conductivity. Zinc alloys are used in the production of small and complex parts due to the low melting point and good casting capability.