Coupling means connecting two parts. In the industry, coupling means a piece that connects two shafts with a base or hard chrome. In simple terms, these devices are mechanical parts that are used to transfer power or torque from one shaft to another shaft.
You may ask what is the reason for using couplings?!
In response, we must say that power can be transmitted with different gear or drive settings only if the shafts are parallel. Coupling is used when the shafts are in a straight line and power is to be transferred from one end of the shaft to the other. Of course, there are different types of couplings that are suitable for transmitting power between two non-parallel shafts (that is, when there is an angle between the two shafts), which we will learn about later.
Different applications of couplings
The main purpose of using couplings is to connect two parts to transfer power from one to the other and finally convert power to movement. For example, we may want to connect a servo motor to a shaft in an industrial machine. Another goal is to absorb inconsistency. In some cases, there may be an error when installing the couplings, or the driver and the part connected to it may not be perfectly level in terms of height or parallelism, which causes more pressure and wear between the parts and, as a result, reduces their useful life. .
In these cases, a coupling absorbs these destructive effects and prevents damage to the parts. In addition, there may be very small errors in the size, dimensions, connections, etc. in the design of industrial parts. In these cases, the use of couplings between these parts reduces the fluctuation in movement and ultimately results in a better and more useful performance. So, in general, the reasons for using couplings can be considered as the following:- To transfer power from one moving shaft to another shaft, the best tool is a coupling.
- Coupling can be used to connect two parts that are produced separately.
- To create more flexibility when transferring power, especially When there is limited space.
- Couplings can be used to reduce shocks and impacts caused by movement between two industrial parts.
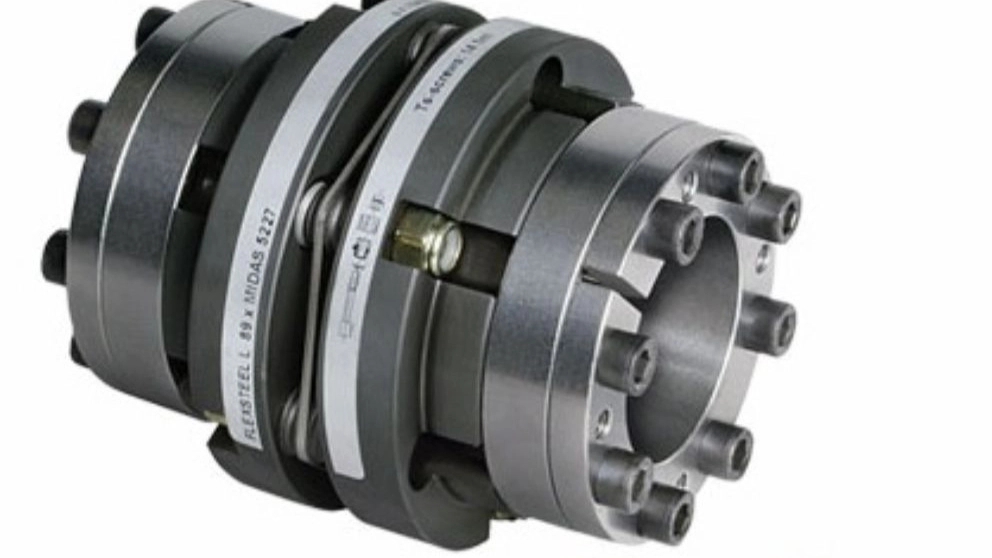
The problems that arise in practice to communicate between two axes have caused different types of couplings to be designed and built to solve these problems.
1- Axial deviation Misalignment
The axes are in the same direction but have a distance in the axial direction, this problem occurs in most couplings due to the temperature changes of the axis and as a result of its longitudinal contraction and expansion, and fortunately Most couplings have the ability to tolerate and neutralize this problem. 2- Radial Misalignment Radial misalignment means that the axes are in a are not extended or during operation according to the working conditions, the axes are distanced from each other in the direction of their radius. It can almost be said that the biggest problem that can cause problems with couplings is radial deviation, because few couplings can overcome this problem. 3- Angular deviation Angular Misalignment
If the axes of the couplings have an angle to each other (or this deviation occurs during operation), we say that the coupling has an angular misalignment. As you will see, many couplings with different models and sizes are used to solve this problem, but in any case, the more the angular deviation is, the more the transmission energy loss between the two couplings will increase.
Introduction of coupling types
Introduction of rigid couplings
Rigid couplings, as their name suggests, have little flexibility. In the construction of this type of couplings, polymer materials are not used, and for this reason, they do not have much ability to absorb vibrations. There are different types of rigid couplings. In the following, we will introduce the types of rigid couplings. Muff Coupling or Muff Clamp Coupling Muff, which is also called a clamp, is a kind of thick hollow cylinder. The design of the muff is such that the shaft fits perfectly in the sleeve. Clamp couplings are produced and supplied in both integral and two-piece forms. Also, to prevent the longitudinal movement of the coupling when connecting two shafts to each other, two or more threaded holes are placed at the ends of the shafts. Muff does not have complicated parts and it is easy to make. Muff coupling is used in cases where the shafts are completely parallel to each other and do not require any alignment, and the load carrying capacity is light to medium. The slotted clamp coupling is divided into two parts. Muffs are semi-cylindrical in shape that are placed on the shafts. To better connect the shafts to each other, threaded holes are created on the slotted clamp coupling so that two shafts can be connected to each other with steel bolts and nuts. The unique feature of this model is that it can be assembled and disassembled without changing the position of the shaft. The use of slotted clamp coupling is to carry medium and heavy loads at a slow speed. Flange coupling (Flange) Flange coupling is one of the most widely used couplings. . The reason for its relatively high use is that the price of this model is low compared to others and of course it has the power to transmit many torques. On both sides of the flanged coupling, an equal number of threaded holes are made to ensure less oscillation of the coupling when the shafts move. Flange couplings are mostly used in medium and heavy industrial applications.