How is charcoal made?
Charcoal is basically produced by burning a carbon-rich material such as wood in a low-oxygen atmosphere. This process removes moisture and volatile gases from the original fuel. The resulting charred material not only burns longer and more stably than solid wood, but is also much lighter (one-fifth to one-third of its original weight). Partially made. One of the main raw materials, which is called coal, is basically traditional coal. As explained above. This material has the ability of briquettes that are easily lit and produce the desired wood smoke flavor. The most desirable raw materials for this component are hardwoods such as beech, birch, hard maple, rosewood and oak. Some manufacturers also use soft woods such as pine or other organic materials and nut shells.
Minor elements include a binding agent (usually starch made from corn, shrimp or wheat), an accelerator (such as nitrate) and an ash bleaching agent (such as lime).
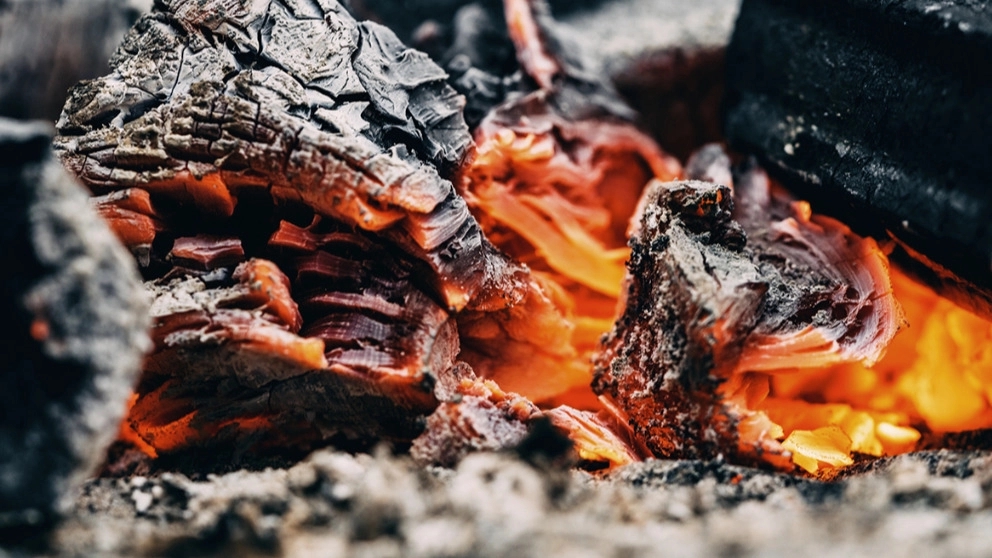
Pressed coal production methods
Some producers use the kiln (batch) method, while others use the continuous (continuous) method.
What is the discontinuous process of how compressed coal is made? In this method, it takes a day or two to load a normal-sized concrete furnace with about 50 cords of wood. When the fire starts, the air inlet and outlet valves are fully open. to absorb enough oxygen to produce a hot fire. Burn over the course of a week. Ports and vents are adjusted to maintain a temperature between about 840-950°F (450-510°C).
At the end of the desired burn period, the air intake doors are closed. The outlet valves are sealed an hour or two later to prevent pressure build-up in the furnace. After a two-week cooling period, the furnace is drained. And carbonaceous wood (coal) powder is produced.
What is the continuous process in how to make compressed coal? In this method, the wood is measured in mill parts. A particle size of about 0.1 in (3 mm) is typical.
Although the exact size depends on the type of wood used (eg, bark, dry sawdust, wet wood). The wood then passes through a large dryer that cuts its moisture content in half (approximately 25%). Next, it feeds it to the top of the furnace
Heat required for the compacted coal production process: From the outside, the chamber looks like a steel silo. It has a height of 40-50 feet (12.2-15.2 meters) and a diameter of 20-30 feet (6.1-9.14 meters). Inside it there is a group of furnaces (three to six depending on the desired production capacity). The upper chamber is the lowest room temperature, which is 525 degrees Fahrenheit (275 degrees Celsius). while the lower chamber burns at about 1,200 degrees Fahrenheit (650 degrees Celsius). External heat comes from burners that use oil or gas. It is needed only in the initial and final stages of the furnace. At the medium level, the evolving gases burn the wood and provide enough heat to maintain the desired temperature level. which exits the central shaft and passes vertically through the entire junction, is stirred. This slow stirring process (1-2 rpm) ensures uniform combustion and moves the material through the confluence. At alternate levels, crawler arms push the burning wood either into a hole around the central shaft or into holes around the outer edge of the floor so that the material can reach the next lower level. As the coal exits the final chamber, it is sprayed with water. turns off cold. It may then be used immediately, or it may be stored in a silo until needed. A typical machine can produce approximately 5,500 pounds (2.5 metric tons) of product per hour
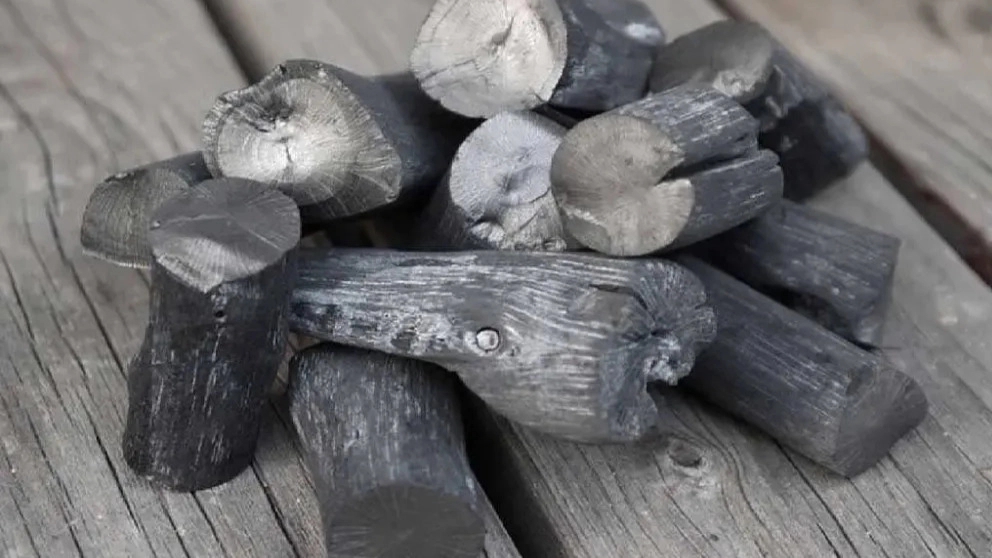
Briquetting and packing: Charcoal and minor materials, including sticky starch, are added to the mixer in appropriate proportions and are thoroughly mixed there. At this stage, the material has about 35% moisture and is somewhat moist like topsoil. The mixed material is released into a press consisting of two opposing rollers containing briquette-sized indentations. Due to the moisture content, binding agent, temperature (about 105°F or 40°C) and the pressure of the rollers, the briquettes retain their shape as they descend from the bottom of the press. The briquettes are dropped onto a conveyor belt, which It transports them through a single pass dryer. and heats them at 275°F (135°C) for three to four hours, reducing their moisture content to about 5%. Briquettes can be produced at different speeds. The briquettes are immediately bagged or stored in silos to await the next packing program. In the case of producing "instant light" briquettes, a hydrocarbon solvent is atomized and sprayed on the briquettes before bagging. Charcoal briquettes are packed in different bag sizes. Some small and convenient packages are made so that the consumer can light the entire bag without removing the briquettes.