What is discontinuous welding?
Interrupted welding, interrupted welding, seam welding and seam welding are the terms used for this welding technique. Discontinuous welding technique means discontinuous welding and only the points where we intend to weld them are welded. In fact, in this method, we will have a weld with a certain length and a step without welding. Intermittent welds have many advantages, the most important of which are the reduction of distortion and skewness, as well as the reduction of the total amount of welding. In addition, since the entire surface is not welded and only some points are welded discontinuously, the welding speed will be very high with this technique. Due to these characteristics, intermittent welding is widely used in welding; Especially when welding speed is a priority. But the thing about discontinuous welding is that less heat is used in this welding. This caused the resistance and durability of the resulting weld to be lower than in other cases.
Discontinuous welding sign in welding
As you know, intermittent welding is one of the most common and practical methods in the welding industry. In this method, there is a gap between the welding operations, which means that after welding one part, a gap is created and then the other part is welded. Placed. In fact, since the type of welding in it is intermittent and segmental, it has become known as intermittent welding. Discontinuous welding, like many welding methods and situations, has its own sign and is displayed as "-".
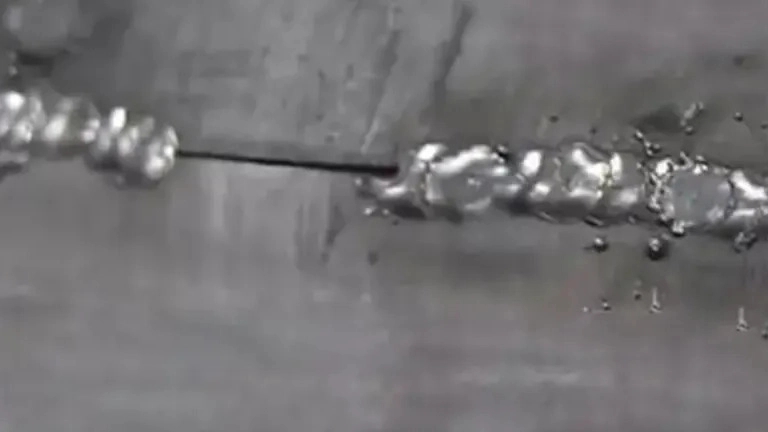
When is it better not to use intermittent welding?
Although discontinuous welding has many advantages, this method also has its own disadvantages. In relation to the disadvantages of discontinuous welding, we can mention its low resistance and its non-use in welding metals with high thickness. Of course, as it is known, the disadvantages of discontinuous welding are very small compared to its advantages and can be ignored. However, it should be noted that intermittent welding should not be used in some cases. In fact, this method should be used when the welder wants to do spaced and non-continuous welding on the part. Also, when a little resistance is needed, this method can be used. Therefore, this method cannot be used in cases such as pipe welding where there should not be any seams. These require continuous welding so that all seams are well covered. Also, when high resistance is needed, it is not permissible to use interrupted welding. Therefore, before starting work, be sure to check the conditions and use the best method for welding.
Get to know the continuous welding technique in welding
Continuous welding is the opposite of discontinuous welding, and as the name suggests, the welding operation is performed continuously and continuously. In fact, in the continuous welding method, there is no gap and welding is done all over. This welding method is used in situations where there are no seams between the welds. For example, this technique should be used in welding pipes and gas or liquid tanks. Because continuous welding, unlike discontinuous, establishes a permanent and continuous connection and prevents material from leaking inside and outside the pipes.
What is the difference between continuous welding and discontinuous welding?
Now that you are familiar with both welding methods, you can easily understand the difference between intermittent welding and continuous welding. However, here we briefly mention the difference between these techniques. That is, first one stitch is done, then a certain distance and then another stitch is done. But continuous welding is not like this and consists of a continuous string of welding. In this method, welding is done in one direction.
- Because of the distance between the interrupted welds, its resistance is lower than that of continuous welding.
- In interrupted welding, less heat is used. is used, which will decrease the strength and durability of the resulting weld.
- Interrupted welding is used in cases such as connecting a nut to a large and flat surface or connecting a belt to narrow parts, and for Welding of pipes is not practical. If the main application of continuous welding is the welding of liquid and gas pipes.
- In butt welding, unwelded gaps reduce the consumption of filler metal. This affects the cost of intermittent welding and causes it to decrease compared to the cost of continuous welding.