What is shotcrete?
Spraying concrete or shotcrete is one of the new ways of implementing concrete structures. In some operational operations such as the implementation of temporary covering of tunnels, restoration operations and the implementation of thin wall structures, or even when the form of work is complex or the molding is difficult and expensive, the use of sprayed concrete (shotcrete (American term) or gunite) English word)} may be the only logical solution. The use of this type of concrete requires experience, special tools and equipment, and experienced workers in concrete spraying.
1. Dry mixed shotcrete
In the dry state, the mixture of stone materials and cement is injected from one side with the help of an air compressor and water from the other side with the help of a pump to the head of a nozzle, and after being mixed together, they are sprayed on the work surface.
This method is used for coating as well as repair works whose thickness is less than 10 cm.
On the other hand, because plain aggregates are not used in this method, this concrete does not have high compressive strength.
Due to the fact that water is added to the mixture only at the last stage, not enough water may reach all the seeds and our mixture, and as a result, the hydration operation will not be performed correctly, so in the continuation of the work, due to the concrete not sticking to the place A large part of it is wasted.
2. More mixed shotcrete
In the wet method, the final concrete mixture is sprayed from the nozzle head with the help of wind. Of course, there are limits on the size of aggregates in concrete spraying. This limit is 10 mm in England. In other words, if the maximum size of the aggregates is smaller than one centimeter, the concrete spraying operation is called gunite, and if it is larger, it is called shotcrete.
Shotcrete implementation tips
In the dry concrete spraying method, which is more common than the wet method, the maximum grain size is generally limited to 10 mm and rarely to 20 mm, which is emphasized in the ninth topic of Iran's national construction regulations. Also, the appropriate weight ratio of aggregate to cement in this method is between 3.5 and 4. In addition, due to the fact that there is no need to inject water in order to transfer the aggregates to the nozzle head in the dry method, generally the final ratio of water to cement is low and as a result, the quality of the process is high. In comparison, if lubricants are used, the ratio of water to cement can be limited to 0.4 in the wet method. The common grade of cement in the fresh method is around 350 to 450 kg/m3. In this case, it is expected that a characteristic resistance of 28 days (cubic samples) between 35 and 55 MPa can be achieved.
Characteristics of sprayed concrete (shotcrete)
Use of fibers in shotcrete
From 1960 onwards, the use of various fibers in shotcrete to reinforce it became common, so that the amount of steel fibers used in shotcrete worldwide in 1970 is estimated at one hundred thousand tons. The dimensions of the fibers used in shotcrete can vary from 12 to 50 mm. The common amount of shotcrete fibers is around 3 to 5 percent by weight. The amount of shotcrete scatter also depends on various factors, including the spraying angle and the distance of the nozzle from the work surface.
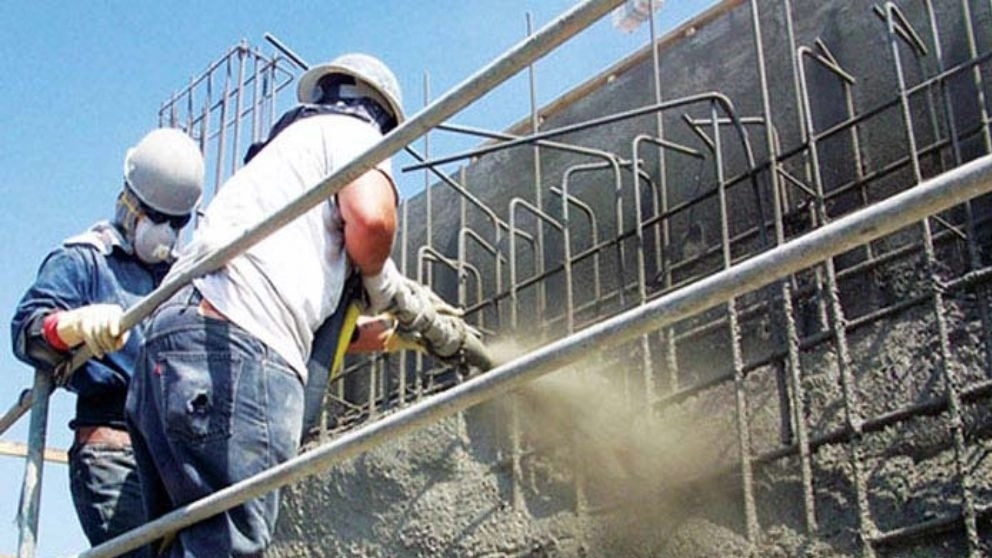