The most common iron and steel melting furnaces used in most factories include bush furnace, cupella furnace, induction furnace and electric furnace. Each of these furnaces has its own unique technology that makes them suitable for different conditions and production capacities.
In addition to the mentioned furnaces that are used to melt metals to make parts, there are other furnaces that are used for extraction Metals are used from their ores. These furnaces include open furnaces, Bessemer furnaces, alkaline oxygen furnaces, and blast furnaces, which are often used for ironmaking and steel production. In the steel production article, learn more about these furnaces and steelmaking methods.
Bush furnace
Bulk furnaces are often used to melt non-ferrous alloys that have a low melting point. The mechanism of these furnaces also includes the use of a refractory ceramic pot so that they can withstand high temperatures. This ceramic pot, which is called a crucible, is placed on top of the heat source to melt the metal and additives in it. The size of these plants is different.
This type of melting furnace has an enclosed structure to keep the heat inside. Commonly used fuels for a bush furnace include coal or natural gas. There are also differences in the design and heating system of furnaces. Apart from mobile and fixed bush furnaces, there are also tilting and fixed bush furnaces. Also, a distinction should be made between furnaces resistant to heating and heating with fuel.
The common types of bush furnaces in casting industries are:
1. Fixed bush furnace: The pot inside this type of furnace is fixed and the molten metal is removed using a valve at the bottom of the furnace.
2. Lifting movable crucible furnace: When the metal in the crucible is completely melted, the crucible is lifted with the help of cranes inside the production site so that the molten metal reaches the molds. Inclined crucible furnace: The crucible inside the furnace is fixed, and the whole furnace system is tilted so that the molten metal comes out of it.
Cupella furnace
Cupella furnace has been used for a long time in various casting industries. The distinctive characteristic of this type of furnace is its high height and cylindrical chimneys. Its interior consists of layers of clay and brick to protect the internal parts from extreme heat, wear and oxidation. This furnace is very suitable for producing high tonnage of melt and is often used for melting cast iron.
For the smelting process as well, several layers of ferroalloys, coke and limestone are charged into the furnace before the base metal is added. they become As a result, these materials react due to heat and are suspended on the molten surface as impurities. The function and efficiency of these additives are:
1. Coke: It is used as a fuel to melt the materials in the furnace. Scrap and alloying elements: The main charge materials that make up the molten metal. Limestone: The addition of this substance, also called flux, causes the ash and other impurities to react with it to form slag. The role of this molten slag, which is placed on the molten metal, is to prevent surface oxidation of the molten metal.
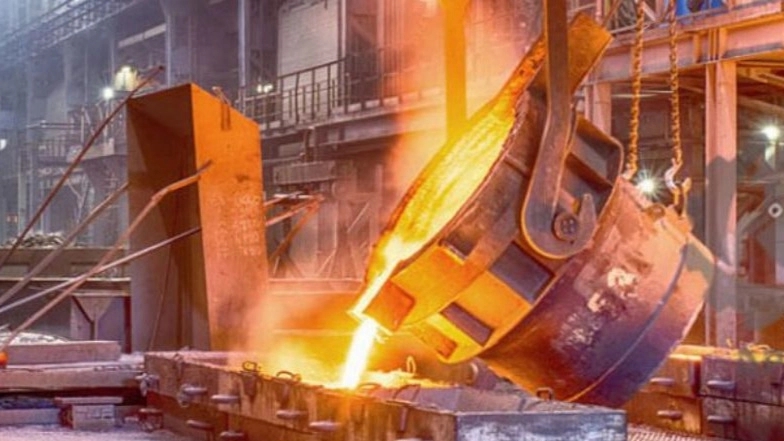
induction furnace
Induction furnaces provide the necessary heat and temperature for melting metals and alloys through alternating electromagnetic current induction technology. This electromagnetic field causes movement in metal atoms, which ultimately leads to heat production. The source of electromagnetic currents are coils or copper coils that are placed around the part but do not have physical contact with it. These types of furnaces are an ideal option for smelting and casting industries due to the production of high quality melt, easy maintenance and very good energy efficiency.