What is the roll forming process?
It is interesting to know that roll forming is a very widely used process, but at the same time it is unknown and unknown. In fact, it can be acknowledged that describing and explaining the role forming process is not an easy task; But in a general situation, it can be acknowledged that the forming of metal sheet strips along straight, longitudinal, parallel bending lines by means of several pairs of contoured rollers without changing the thickness at room temperature is called roll forming process.
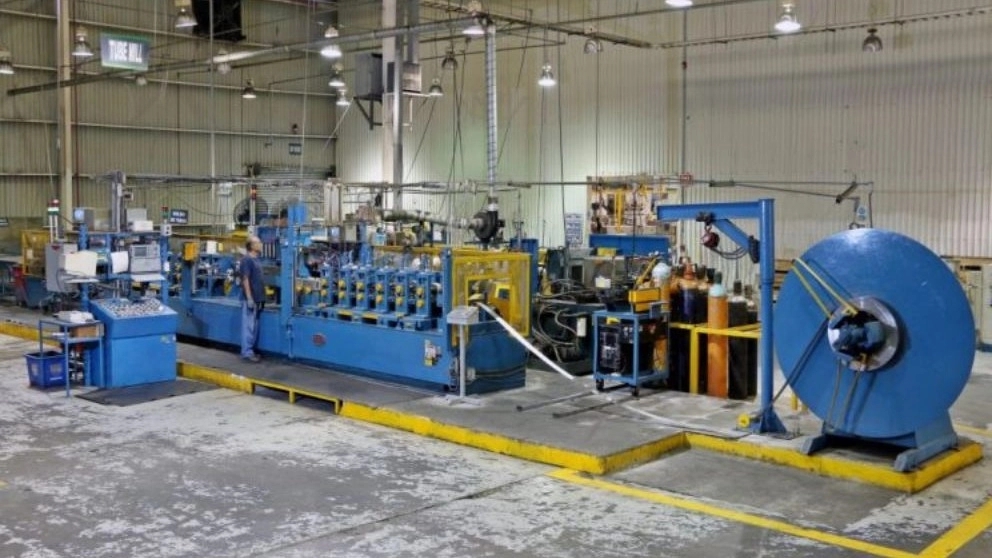
Roll forming process and related details
In general, it can be acknowledged that roll forming is always mentioned as a widely used and important process because this process has grown as the most efficient metal forming technology during the last half century. In fact, it is interesting to know that about 35 to 45 percent of all steel produced by American factories was produced by the roll forming process, which is more than the steel used in the automotive industry. Considering this issue, it can be acknowledged that daily hundreds of devices, cars, buildings, agricultural machinery, tanks and other products are produced by the roll forming process, but most of the people who are outside this profession have even the slightest knowledge of this industry. do not have During the 100-year history of roll forming, thousands of tools, equipment, designers and users have worked and are still working in this industry, but unfortunately, much of the experience gained by operators, equipment installation engineers and designers has never been documented and recorded. have not been Therefore, from all the research articles and reports, only a limited number can be interpreted and applied in the roll forming industry. Examining the sheet roll forming process is not an easy task. The international definition given for the roll forming process fully shows the complexity of this case.
• Products produced by sheet roll forming often have curves.
• The angle of the bending lines can be 90 degrees.
• Bending lines are not always straight and sometimes this happens on purpose. On the other hand, the bending lines are not always parallel, and this is often done deliberately and at the request of the customer.
• It should be noted that the thickness of the sheet always decreases in the bent parts or in other words the bending lines.
Also, the rollers of the sheet roll forming machine have special passages that can reduce the thickness of the sheet wherever necessary. Also, in curved products that are thin, the outer threads and ridges are formed thinner than the inner ridges.
On the other hand, it is mentioned in the above definition that the temperature of the environment does not change during the work, but:
• Metal sheets are heated before roll forming to prevent paint cracking in bending lines.
• The operation temperature should be increased for the sheets that have been soldered, annealed or brazed.
Getting to know the vacuum forming machine and its types
Vacuum forming is often used to shape plastic sheets. This operation is associated with the application of direct or induction heat. In fact, in this operation, after the sheet is placed in the sheet holder part of the machine, the heater applies direct heat to the sheet. In this state, the sheet becomes a dough, the mold approaches the sheet, and the air between the sheet and the forming machine is discharged. to be Of course, it should be noted that this process can be used for soft sheets.
Types of vacuum forming methods include the following:
• Vacuum forming
Vacuum forming or vacuum forming refers to sheets softened by heat, which is caused by direct or induced heat and the evacuation of air between the sheet and the mold, which makes the sheet formable like a mold. In general, in this process, first the heat-sensitive plastic sheet (thermoplast) is heated to a certain extent to become soft and flexible, then this sheet is softened and placed on the mold with the help of air vacuum and stretched on the mold, and the shape of the mold is made. takes on In fact, the thermoforming process takes place in two stages: heating and shaping, in the heating stage, the plastic sheets are placed at a certain distance from the heating elements and become soft, and in the second stage, the shape of the flexible sheets is formed on the hollow molds. They say that the vacuum in the mold causes the plastic to be pulled into the mold. After forming and hardening the plastic sheet, finally the piece is separated from the mold and the extra parts are cut.
• Forming with air pressure
In this method, the flexible plastic sheets are applied by air pressure from above on the mold sheet. In this case, the sheet is pulled into the cavity of the mold. It is necessary to explain that in order to expel the air that is trapped between the sheet and the mold, holes must be installed in the mold so that the forming process with air pressure can be operated in the best way.
• Mechanical shaping
In this method, the heat-sensitive plastic sheet is placed between the positive and negative parts of the mold. Finally, it presses the plastic mechanically with direct force from the positive part of the mold and the sheet is drawn into the cavities of the negative mold. In this regard, it should be mentioned that one of the most prominent advantages of this method is the better dimensional accuracy of the product and the more accurate geometric details on both sides of the piece compared to the other two methods, and the only problem with this method is that it requires two positive and negative parts. It is a mold that results in high production costs.
Getting to know the types of roll forming systems
The most important member of a roll forming line is the rolling machine. Because the rolling machine applies the necessary force and support to the rollers, which causes the metal to be shaped. It is interesting to know that in this field, the variety in the design of rolling machines is unlimited, but they can be classified into the following categories, among which are types of suspended, duplex, combined duplex, standard and plate machines. It should also be noted that devices that are not included in any of the above categories can be considered special rolling devices.
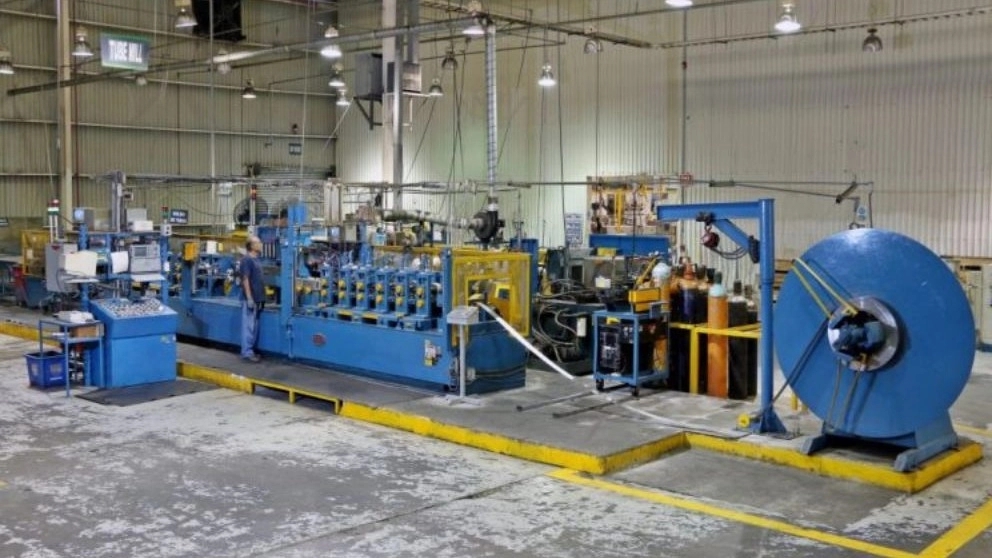
Familiarization with various sheet roll forming methods
In order to obtain an effective and practical product, we have always seen different procedures in every process to obtain the output. In this regard, the methods of roll forming of sheets exist in different ways, and according to this issue, the types of roll forming methods can be considered as including the following:
1. Cold roll forming method
In a more general view, it can be stated that sheets that are produced through hot rolling with minimum thickness are usually subjected to acid washing, thickness reduction or shape change through cold rolling process. . In fact, it can be said that the application of cold rolling is to reduce the thickness with the desired dimensional accuracy of steel sheets. Also, in this cold roll forming process, it is possible to mention the straightening of the sheets during the operation, in this way, the roller that includes two small diameter rollers removes the curvature of the sheet that was created in the previous process and It is smooth as it comes out of the roller. In fact, the purpose of cold roll forming is to reduce the thickness of the sheet under very high pressure, which is usually done at room temperature and up to 200 degrees Celsius. In this cold method, for the success of the process, things such as the characteristics of the sheet roll forming machine, the skill of the tool designer, the quality and performance of the designed tool, the skill of the operator, the way the tool is placed, and the formability of the sheet strip are influential. The application of this process in the sheet metal industry is very diverse, so that it covers a range of parts with low precision to sensitive and precise parts.
2. Hot roll forming method
The hot method is used for forming thick sheets. In general, in this method, the temperature of metal sheets is raised to a very high level to help form thick sheets. Hot rolling has fewer fans than cold rolling, and the products produced by this method have limited practical uses. Products such as beams, corners or thick formed sheets such as plates are rolled by hot rolling method. Performing sheet roll forming operation by hot rolling method requires great accuracy in setting the desired temperature, as temperature change, low and high temperature may lead to the destruction of the products. This is why only a few factories use the hot rolling method.