What is bronze?
The history of bronze goes back thousands of years and today this copper alloy has many applications in various industries. Bronze was produced and prepared before 3000 BC; However, until years later, this metal was not used to make various artifacts. The ratio of copper and tin is very different (from 67% to 95% copper has been discovered in ancient works).
In one of the Greek manuscripts from the 11th century AD, an alloy with a ratio of 1 pound of copper and 2 ounces of tin (8 to 1 ratio) is mentioned; Over time, this approximate ratio was used to make bronze weapons. Some modern bronze metals are completely free of tin and in their composition you will see other metals such as aluminum, manganese and even zinc.
What metals is bronze made of?
In general, an alloy of copper that includes zinc is considered "brass"; However, the presence of tin (less than 11%) in copper alloys is one of the hallmarks of "bronze". The composition of bronze can be very variable. Currently, modern bronze, whether tin-containing or tin-free, usually contains silicon (Si), manganese (Mn), aluminum (Al), zinc (Zn), and other metals.
"Raw" bronze is almost pink or salmon-colored; However, you will rarely see this metal in its pure state. In most cases, corrosion and patination of bronze causes the color of this metal to vary from lime green to dark brown. When exposed to the air, bronze will be constantly changing and will oxidize and corrode as it goes through different stages. The beginning of each of these stages depends on various factors. Some of these factors are:
Bronze composition
Patination or other protective operations that are applied to the metal during production.
the weather
Installation location and duration of metal contact with rain, sun and other weather conditions
Atmospheric pollutants
Scheduled cleaning and maintenance
Adjacent materials including sedimentary materials
Introduction of bronze types
In addition to tin, other metals such as manganese, aluminum, nickel, phosphorus, silicon, arsenic or zinc are also used to make different types of bronze. Each of these metals gives unique characteristics to bronze.
The most common types of bronze and their characteristics
Aluminum bronze: by adding 6 to 12 percent aluminum to the main copper-tin composition, bronze can be produced, which, in addition to greater strength, will also be more resistant to corrosion; This copper alloy is known as aluminum bronze. This metal is one of the most widely used elements in various fields, including construction and mechanics.
Some of the valuable properties of aluminum are: high irregular reflection, low secondary heat emission coefficient and good conductor of heat and electricity. After combining aluminum with bronze alloy, all these features will be transferred to the new combination.
Manganese bronze: This alloy has good mechanical properties and high fatigue resistance. In general, manganese bronze is suitable for parts that require resistance to pressure, wear and fatigue.
Nickel bronze: This alloy has high resistance to corrosion and oxidation. For this reason, nickel bronze is suitable for applications dealing with corrosive environments, such as a variety of valves and marine components.
Phosphor bronze: This bronze is formed by adding phosphorus to it and has good features such as resistance to wear and corrosion. Phosphor bronze is used as a construction alloy and in industries that require wear resistance.
Silicon bronze: Copper silicon bronze is formed by adding silicon to it. This alloy has high resistance to wear and pressure and is suitable for parts that are in contact with corrosive substances in harsh conditions, such as machine parts and pump parts.
The use of bronze types
Art: One of the main uses of bronze is likely to be found in art, especially as a primary material for sculpture. Bronze's very slow shrinkage when cooled makes it a favorite metal for sculptors who display their art using metals. Contrary to the high weight and high density of this alloy, it is very easy to work with it and is one of the preferred options for sculptors.
In most cases, sculptural bronze is used to make outdoor sculptures. Since the casting of this metal is done with ease, there is almost no limit in the shapes and forms obtained from it. The most common forms made with bronze include the human figure, landscapes, battle scenes, animals, weapons, decorative elements (including stars and flowers) and various plaques.
Construction: In most construction projects today, steel is considered as an alternative to bronze, however, bronze is still used in some cases. For example, many components of drawbridges, worm drive wheels and turntables of bridges are made using a special type of bronze.
In addition, bronze is also used to make modern safety tools, including hammers and wrenches. These tools are usually made of steel, but the danger of fire and explosion caused by sparks released from metal tools made bronze to replace steel.
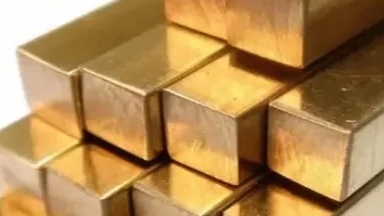
Structural bronze is usually used to make the following:
Door and window frames
Metal parts of doors and windows
Mailbox and gutter
Pleats or rails
Metal furniture
In contrast to the patina-like appearance of sculptures and exterior decorations made with bronze, architectural components are designed to retain the natural, polished, "pink" appearance of raw bronze. This is only possible with continuous polishing and oiling of bronze construction and decorative components, or using transparent varnishes that must be renewed at specific intervals.
Design of devices
A significant number of components of various devices are made using bronze (such as gears, bushings, bearings, valve components and even valve guides in aircraft engines) because this metal, in addition to its high thermal resistance, is a good conductor of electricity. and has little friction. Few metals have low friction; But this feature is important for preparing components that are moving and slide against each other at high speeds.