What is rolling?
Rolling is basically a metalworking process that uses a lot of mechanical forces to change the shape and size of the metal. Usually, this process involves passing metals through a series of rollers that apply high compressive forces to the metal and cause it to change shape. In other words, the meaning of rolling is to enter metals into a rolling mill and make changes in its shape or size. A rolling mill, also known as a rolling machine, consists of two or more rollers that rotate in opposite directions and cause metals to be pressed. This pressure changes the size and shape of the metal and makes it into your desired shape. Metal in this process may be converted into sheet, plate, rod, pipe or various structural sections that are used in industries such as construction, automotive, aerospace, manufacturing and infrastructure.
How has the history of rolling been?
The history of rolling dates back to ancient civilizations thousands of years ago. At that time, the metals were heated and then by impact and pressure, they made its diameter as desired. In fact, it was the rolling technique that was done for the first time. This was done with difficulty and frequent blows until the water mill was invented around the third century BC. These mills caused pressure to the metal by rotating large stones and by reducing the diameter of the metal, it led to an increase in its length. With the passage of time, these mills made significant improvements and found a wide application in the production of metal products. Until the industrial revolution happened and steam engines were invented by James Watt. This invention led to the construction of larger rolling machines and the use of water mills.
With the passage of time, wonderful discoveries and developments happened in the field of iron and steel, which also improved the rolling process. These developments reached the point where today rolling machines are automatic and roll automatically. This has led to the production of a wide range of steel products with precise dimensions and high quality to meet the needs of various industries. As a result, the history of steel rolling has spanned centuries and witnessed significant technological advances. . This path started from manual forging and after passing through water mills and rolling machines with steam engine, it has reached modern automatic systems.
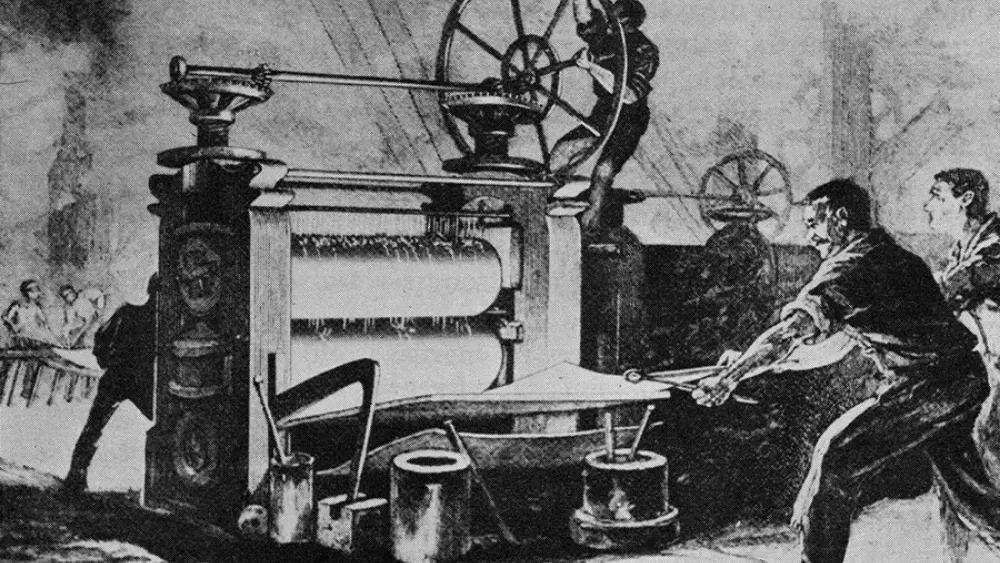
What is a rolling machine?
The rolling machine is a mechanical device that is used to convert ingots into sheets. After that, this device can be used to change the length, width and diameter of the sheet. Of course, by changing the angle of the rollers relative to each other, it can also be used to bend steel sections. The application of this device is usually in various industries such as metalworking, construction and production. The general operation of the rolling machine is to pass the metal through two or more rollers that rotate in opposite directions. The rollers, which have a distance less than the diameter of the metal, press it and change its length, width and diameter.
Rolling machines are available in various sizes and configurations and have manual, semi-automatic or fully automatic controls depending on the complexity and accuracy required. Rolling machines have many advantages in metalworking operations, the most important of which is their high accuracy and repeatability. Of course, we should not forget that to use manual or semi-automatic rolling machines, skilled operators are needed who are familiar with its functional and security protocols. Because each type of rolling operation has its own processes and instructions and requires a certain accuracy and speed.
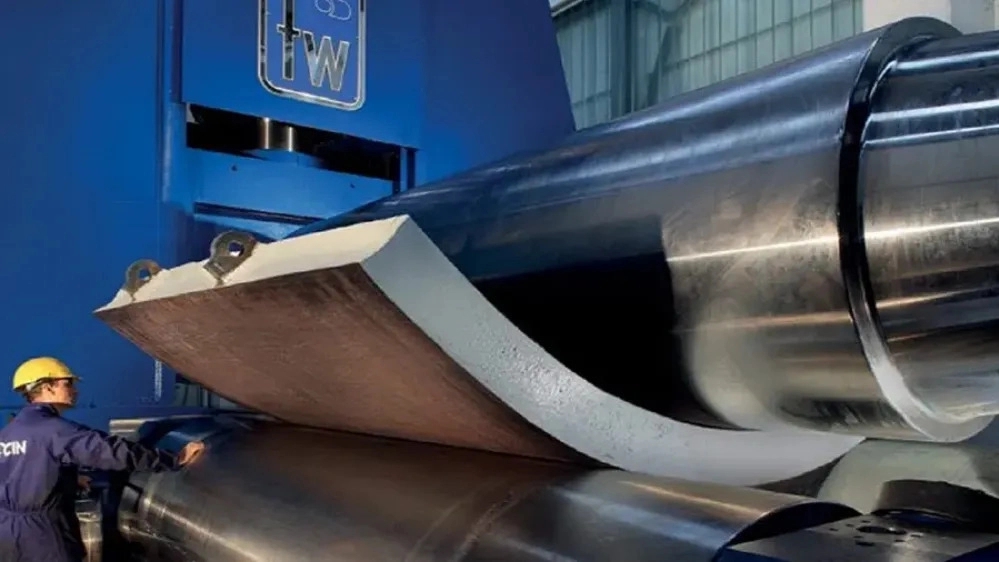
Rolling types
Rolling can be classified from three perspectives, which we will discuss below.
Types of rolling in terms of temperature
1. Hot rolling: Heating metals to a temperature higher than the recrystallization temperature and then passing it through rolling rollers is called hot rolling. The recrystallization temperature is the temperature at which deformed metal grains transform into new grains, and this position makes the metal easier to form during rolling. Hot rolling is usually done above this temperature to reduce its resistance to deformation in addition to its flexibility. This temperature is different for different metals and alloys. For example, for steel between 1100 and 1300 degrees and for aluminum between 300 and 600 degrees Celsius. When the metal reaches this temperature, it is ready to pass through the rollers. When the metal passes through the rollers, a certain pressure is applied to it so that its thickness is reduced and it takes the desired shape. This rolling is used to produce plates and sections that are used in various industries including construction.
2. Cold rolling: After hot rolling, we leave the metal alone until it reaches room temperature. Then, to remove the appendages and scales created on the surface of the metal, we acid wash it. Now, our metal piece is ready for cold rolling and enters the machine. The acid-washed metal passes through two rollers that have a distance less than the thickness of the metal. This happens to reduce the thickness of the piece and add to its length. The created product has advantages such as beautiful appearance, accurate tolerance, easy transportation and high tolerance and resistance. This rolling is used to produce sheets, strips, foils and precision parts.