Plastik enjeksiyon makinesi nedir?
Günümüzde imalat sanayinde plastik enjeksiyon makinelerinin kullanımı oldukça yaygın hale gelmiştir. Plastik, fiyatının iyi olması ve kolay şekillendirilebilmesi nedeniyle insan yaşamında neredeyse en büyük payı bulmuş ve otomobil imalatı, elektronik, havacılık ve uzay, ilaç, inşaat, oyuncak vb. sektörlerde kullanılmaktadır. . Bu sektörün bol kârı nedeniyle pek çok hayran kazandı.
Plastik enjeksiyon makinesinin tarihçesi
Plastiğin ömrünün üzerinden yaklaşık yüz yıl geçti. Yaklaşık yetmiş yıl öncesine kadar bu sektörün bugünkü şekli ve kapsamıyla varlığından kimsenin haberi yoktu. Selüloz doğadan elde edilen ve insanlar tarafından kullanılan ilk sözde plastik malzemelerden biridir. Orman ağaçlarının sakızından sanayide kaoutcho adı verilen bir madde kullanılıyordu. 1870 civarında selüloz asetat malzemelerinin işletilmesi başladı. 1906 yılından 1909 yılına kadar B. Kland isimli bir kişi, endüstriyel kimya yoluyla ilk plastik malzemeyi hazırlamayı başardı ve bu plastik, Bakalit adıyla anılmaya başlandı. İlk kez John Wesley Haight, 1868'de bilardo topları üretmek için kalıba selüloit enjeksiyonu kullandı. Wesley, selüloidi optimize ederek onu işlenmeye ve son şekli vermeye hazır hale getirdi. Günümüz makinelerinden daha basit ve daha az bileşene sahip olan ilk enjeksiyon makinesi 1872 yılında John ve kardeşi tarafından yapılmıştır. John tarafından yapılan cihaz, malzemeyi ısıtılmış silindirden geçiren ve kalıba enjekte eden bir pistona sahiptir. Sektörün yıllar geçtikçe yavaş ilerlemesiyle birlikte gömlek yaka şekillendiricileri, düğmeler ve cep omuzları gibi başka ürünler de üretildi. 1940'larda, II. Dünya Savaşı sırasında ucuz ve seri üretilen ürünlere olan büyük talep nedeniyle enjeksiyon kalıplama konsepti önemli bir büyüme kaydetti.
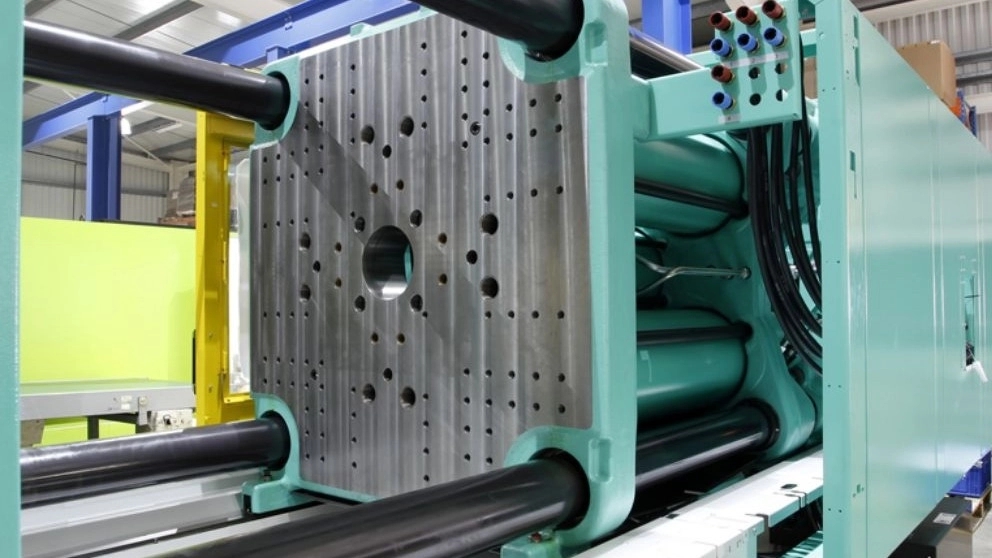
1946'da James Hendry ilk vidalı enjeksiyon makinesini icat etti ve plastik endüstrisinde devrim yarattı. Cihazında pistonun yerini tasarlanmış bir matkap aldı. Bu matkap, malzemeleri enjeksiyondan önce silindirin içine yönlendiriyor, karıştırıyor ve ardından kalıba koyuyordu. Bu sayede enjeksiyon operasyonundan önce renkli veya geri dönüştürülmüş plastiğin hammaddelerle birleştirilmesi ve karıştırılması imkanı tamamen mümkün oldu. Bugün ilgili firmaların üretim payının %95'ini spiral enjeksiyon makineleri oluşturmaktadır. Enjeksiyon kalıpları endüstrisi uzun yıllar boyunca yavaş yavaş omuz ve düğme üretiminden medikal, havacılık, oyuncak, ambalaj, otomotiv ve inşaat ürünleri üretimine doğru gelişmiştir. Bir parça mühendis veya endüstriyel tasarımcı tarafından tasarlandıktan sonra kalıpçı tarafından parçaya göre kalıp yapılır. Enjeksiyon kalıpları genellikle çelik veya alüminyumdan yapılır ve tasarlanan parçanın özelliklerini yansıtacak şekilde özenle işlenir. Enjeksiyon kalıplama, en küçük nesnelerden otomobillerin tüm gövdesine kadar geniş bir ürün yelpazesi üretmek için kullanılır.
Plastik enjeksiyonun yetenekleri ve sınırlamaları
Plastik enjeksiyon, yüksek hacimlerde aynı plastik parçaların üretilmesi için en uygun maliyetli teknolojidir. Plastik enjeksiyon için çok çeşitli hammaddeler mevcut olup, bu malzemelerin fiziksel özellikleri tasarımınızın gereksinimlerine göre özelleştirilebilir. Plastik enjeksiyon, üreticilere yüksek üretim hızının yanı sıra yüksek tekrarlanabilirlik de sağlar (bir üretim döngüsü genellikle 60 saniyeden az sürer).
Plastik enjeksiyon parçalarında kaynak çizgilerinin nedeni
Parçada çok sayıda delik var. Parçada plastik enjeksiyon akışını kesintiye uğratan birçok detay bulunmaktadır. Erimiş plastik birkaç kapıdan kalıba enjekte edilir. Bu sorunları önlemek için delik sayısını sınırlamak veya daha viskoz plastik bileşikler kullanmak daha iyidir. Plastik enjekte edilirken parçanın ölü kısımlarında (tek tarafı kapalı olan kısımlarda) hava sıkışabilir ve hava basıncı plastiğin parçanın içine akışını engeller. Bu sorun parçanın bazı bölgelerinin tamamen sıkıştırılmış plastikle dolmamasına neden oluyor. Parça içinde sıkışan bu havanın sıcaklığı yükselerek parçanın bazı kısımlarını yakabilir. Kritik noktalara havalandırma delikleri eklenerek bu sorunun önüne geçilebilir.